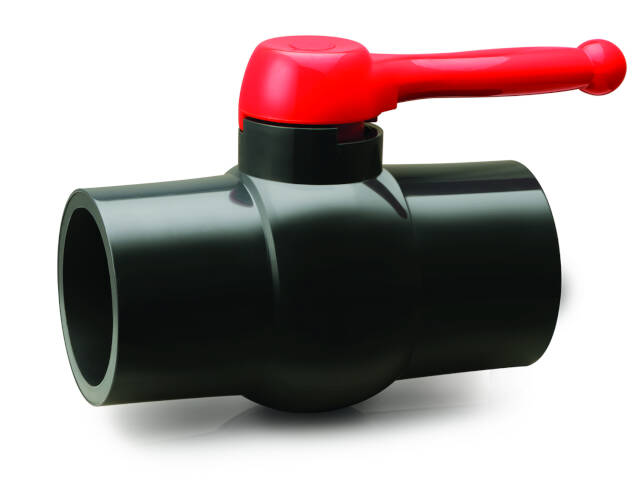
Tecza UPVC pipes are made from highest grade quality resin. These pipes & fittings are mainly used for water supply in agriculture, drip irrigation & sprinkler lines etc. as well as for drinking water distribution. However, these can also be used in cable ducting, ventilation pipe lines, & slurry lines etc.
Size (in mm) | Standard Packing | |
---|---|---|
6Kg | 10Kg | |
20mm | - | 80 |
25mm | - | 55 |
32mm | - | 35 |
40mm | 35 | 20 |
50mm | 20 | 15 |
63mm | - | - |
75mm | - | - |
90mm | - | - |
110mm | - | - |
125mm | - | - |
140mm | - | - |
160mm | - | - |
180mm | - | - |
200mm | - | - |
225mm | - | - |
250mm | - | - |
280mm | - | - |
315mm | - | - |
355mm | - | - |
400mm | - | - |
Size (in mm) | Standard Packing |
---|---|
20mm | 45 |
25mm | 30 |
32mm | 20 |
40mm | 15 |
50mm | 12 |
Nominal Outside Diameter (Nominal Size) |
Mean Outside Diameter | Outside Diameter at any point | Wall Thickness | Mean Socket Internal Diameter of Mid Point of Socket Length | ||||||||||||||
---|---|---|---|---|---|---|---|---|---|---|---|---|---|---|---|---|---|---|
Class 1 0.25 MPa 2.5 Kg/cm2 |
Class 2 0.40 MPa 4.0 Kg/cm2 |
Class 3 0.60 MPa 6.0 Kg/cm2 |
Class 4 0.80 MPa 8.0 Kg/cm2 |
Class 5 1.00 MPa 10.0 Kg/cm2 |
Class 6 1.25 MPa 12.5 Kg/cm2 |
|||||||||||||
Min | Max | Min | Max | Min | Max | Min | Max | Min | Max | Min | Max | Min | Max | Min | Max | Min | Max | |
20 | 20.0 | 20.3 | 19.5 | 20.5 | - | - | - | - | - | - | - | - | 1.1 | 1.5 | 1.4 | 1.8 | 20.1 | 20.3 |
25 | 25.0 | 25.0 | 24.5 | 25.5 | - | - | - | - | - | - | 1.2 | 1.6 | 1.4 | 1.8 | 1.7 | 2.1 | 25.1 | 25.3 |
32 | 32.0 | 32.3 | 31.5 | 32.5 | - | - | - | - | - | - | 1.5 | 1.9 | 1.8 | 2.2 | 2.2 | 2.7 | 32.1 | 32.3 |
40 | 40.0 |
40.3 |
39.5 | 40.5 | - | - | - | - | 1.4 | 1.8 | 1.8 | 2.2 | 2.2 | 2.7 | 2.8 | 3.3 | 40.1 | 40.3 |
50 | 50.0 | 50.3 | 49.4 | 50.6 | - | - | - | - | 1.7 | 2.1 | 2.3 | 2.8 | 2.8 | 3.3 | 3.4 | 4.0 | 50.1 | 50.3 |
63 | 63.0 | 63.3 | 62.2 | 63.8 | - | - | 1.5 | 1.9 | 2.2 | 2.7 | 2.8 | 3.3 | 3.5 | 4.1 | 4.3 | 5.0 | 63.1 | 63.3 |
75 | 75.0 | 75.3 | 74.1 | 75.9 | - | - | 1.8 | 2.2 | 2.6 | 3.1 | 3.4 | 4.0 | 4.2 | 4.9 | 5.1 | 5.9 | 75.1 | 75.3 |
90 | 90.0 | 90.3 | 88.9 | 91.1 | 1.3 | 1.7 | 2.1 | 2.6 | 3.1 | 3.7 | 4.0 | 4.6 | 5.0 | 5.7 | 6.1 | 7.1 | 90.1 | 90.3 |
110 | 110.0 | 110.4 | 108.6 | 111.4 | 1.6 | 2.0 | 2.5 | 3.0 | 3.7 | 4.3 | 4.9 | 5.6 | 6.1 | 7.1 | 7.5 | 8.7 | 110.1 | 110.4 |
125 | 125.0 | 125.4 | 123.5 | 126.5 | 1.8 | 2.2 | 2.9 | 3.4 | 4.3 | 5.0 | 5.6 | 6.4 | 6.9 | 8.0 | 8.5 | 9.8 | 125.1 | 125.4 |
140 | 140.0 | 140.5 | 138.3 | 141.7 | 2.0 | 2.4 | 3.2 | 3.8 | 4.8 | 5.5 | 6.3 | 7.3 | 7.7 | 8.9 | 9.5 | 11.0 | 140.2 | 140.5 |
160 | 160.0 | 160.5 | 158.0 | 162.0 | 2.3 | 2.8 | 3.7 | 4.3 | 5.4 | 6.2 | 7.2 | 8.3 | 8.8 | 10.2 | 10.9 | 12.6 | 160.2 | 160.5 |
180 | 180.0 | 180.6 | 177.8 | 182.2 | 2.6 | 3.1 | 4.2 | 4.9 | 6.1 | 7.1 | 8.0 | 9.2 | 9.9 | 11.4 | 12.2 | 14.1 | 180.2 | 180.5 |
200 | 200.0 | 200.6 | 197.6 | 202.4 | 2.9 | 3.4 | 4.6 | 5.3 | 6.8 | 7.9 | 8.9 | 10.3 | 11.0 | 12.7 | 13.6 | 15.7 | 200.3 | 200.6 |
225 | 225.0 | 225.7 | 222.3 | 227.7 | 3.3 | 3.9 | 5.2 | 6.0 | 7.6 | 8.8 | 10.0 | 11.5 | 12.4 | 14.3 | 15.3 | 17.6 | 225.3 | 225.7 |
250 | 250.0 | 250.8 | 247.0 | 253.0 | 3.6 | 4.2 | 5.7 | 6.5 | 8.5 | 9.8 | 11.2 | 12.9 | 13.8 | 15.9 | 17.0 | 19.6 | 250.4 | 250.8 |
280 | 280.0 | 280.9 | 276.6 | 283.4 | 4.1 | 4.8 | 6.4 | 7.4 | 9.5 | 11.0 | 12.5 | 14.4 | 15.4 | 17.8 | 19.0 | 21.9 | 280.4 | 280.9 |
315 | 315.0 | 316.0 | 311.2 | 318.8 | 4.6 | 5.3 | 7.2 | 8.3 | 10.7 | 12.4 | 14.0 | 16.1 | 17.3 | 19.9 | 21.4 | 24.7 | 315.4 | 316.0 |
355 | 355.0 | 356.1 | 350.7 | 359.3 | 5.1 | 5.9 | 8.1 | 9.4 | 12.0 | 13.8 | 15.8 | 18.2 | 19.6 | 22.6 | 24.1 | 27.8 | 355.4 | 356.0 |
400 | 400.0 | 401.2 | 395.2 | 404.8 | 5.8 | 6.7 | 9.1 | 10.5 | 13.5 | 15.6 | 17.8 | 20.5 | 22.0 | 25.3 | 27.2 | 31.3 | 400.4 | 401.0 |
Note: Pipes available with ISI mark except 400mm.
Fittings | Pipes | |
---|---|---|
Material | Unplasticized Polyvinyl Chloride(UPVC) |
Unplasticized Polyvinyl Chloride (UPVC) |
Colour | Light Grey | Light Grey |
Refernce Standards | IS 7834 : 1987 | IS 4985 : 2000 |
Working Temperature of fluids | Upto 60 degree- Continous Upto 90 degree- Short Time -upto 3 mins |
Upto 60 degree- Continous Upto 90 degree- Short Time -upto 3 mins |
Working Temperature (gk/cm2) | 4, 6, 10 & 16 | 2.5, 4, 6, 10 & 12 |
End Connections | Solvent sockets, Threads (For transition fittings) |
Solvent sockets, Rubber Ring sockets |
It is imperative to mark the pipe from all sides so that pipe is cut with the help of a Hand Saw. It should be a right angle cut from all the sides. The cut piece should not be with burr on edges.
Remove all the burrs and ridges accumulated on the inner as well as the outer edges of the pipe with the help of a deburring knife, file or abrasive paper.
Thoroughly clean the pipe with dry cloth where the solvent cement is going to be applied, to avoid dust, dirt, oil, moisture and other foreign material during the installation process.
After cutting, the pipe needs to be chamfered from the outer sides. It is advisable to provide approximately2 mm wide, 150 chamfer on spigot end.
Before applying solvent cement, insert the pipe end into the socket of the next pipe or fitting to check that interference occurs at about 1/3 to 2/3 of the socket depth.
Mark the pipe length to be inserted for jointing. Apply a liberal coat of solvent cement with the help of the brushon the marked surface.
Push the pipe inside the fitting so that it goes inside it equally from all the sides. Wipe off excess solvent cement that comes out from all the edges. Hold the joint for to 2 minutes so that the jointing is perfect.
Pipe line should be installed in proper alignment and along with necessary clamps.
Pressure testing to be done before concealing work.
Pressure testing may be carried out after a curing period of 24 hrs.
Do not cut slant/unevenly.
Do not proceed with the installation of pipe without deburring.
Do not join the pipes without cleaning the pipe ends.
Do not proceed with installation of pipe without chamfering.
Do not apply solvent cement without dryfit test.
Do not apply excess solvent cement on the pipe and do not use solvent cement by hand.
Do not use a hammer or half push the pipe.
Don't over tighten with pipe wrench.
Avoid loose joints and misalignments.
Pressure testing should not be done before 24 hrs of curing.